#4 in a series of articles about the technology behind Bang & Olufsen loudspeakers
This week we’ll look at how most loudspeakers in the Bang & Olufsen go from the original idea through to the final product. I’ll use the BeoSound 8 (nowadays called the BeoPlay A8) as an example of this development process. However, the process itself is almost identical for almost all of our products.
The concept
The first step with most (but certainly not all) of our loudspeakers is an idea from either a designer or someone from our product definition department. They’ll come to the acoustics department with an idea of the product concept. This includes things like the following
- what kind of loudspeaker is it? (i.e. a docking station, a “bookshelf” loudspeaker, a floor-standing loudspeaker, etc.)
- the target customer and usage
- the target price
- a rough idea of the size and shape
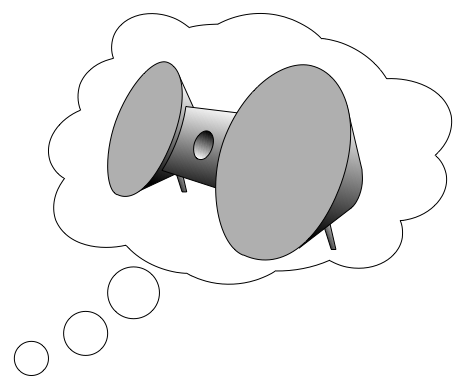
From there, the acoustics engineer for the project can start looking into what kind of hardware we should use for the project. For example, this means things like:
- how many loudspeaker drivers (i.e. is it a single “full range” driver, a 2-way, a 3-way or something else?)
- loudspeaker driver dimensions (i.e. diameters and depths)
- how much volume we have in the enclosure behind the driver(s)
Based on this, we get a “best guess” of what kind of system we’re looking at – at least with respect to the acoustics. At this point, if the acoustic engineer thinks that it’s a feasible concept, then we’ll move on to building a first prototype. If not, then we’ll enter into meetings with the product definition and design people to start working out the issues. However, for this story, let’s assume that all is well, and we can keep moving on.
Prototype #1
In order to get some idea of the acoustic performance of the system (basically meaning “can it play bass loudly enough?”) a first prototype is constructed. This is almost always a box made of MDF with a reasonable guess of the internal enclosure volume. Typically, at this point, we’ll use some off-the-shelf loudspeaker drivers that have roughly the same size and characteristics as what we’ll need in the product. In the case of the BeoSound 8, that first prototype looks like the one shown in the photo below. This prototype looks like it’s one box, but there is a bulkhead separating the two volumes behind the woofers.
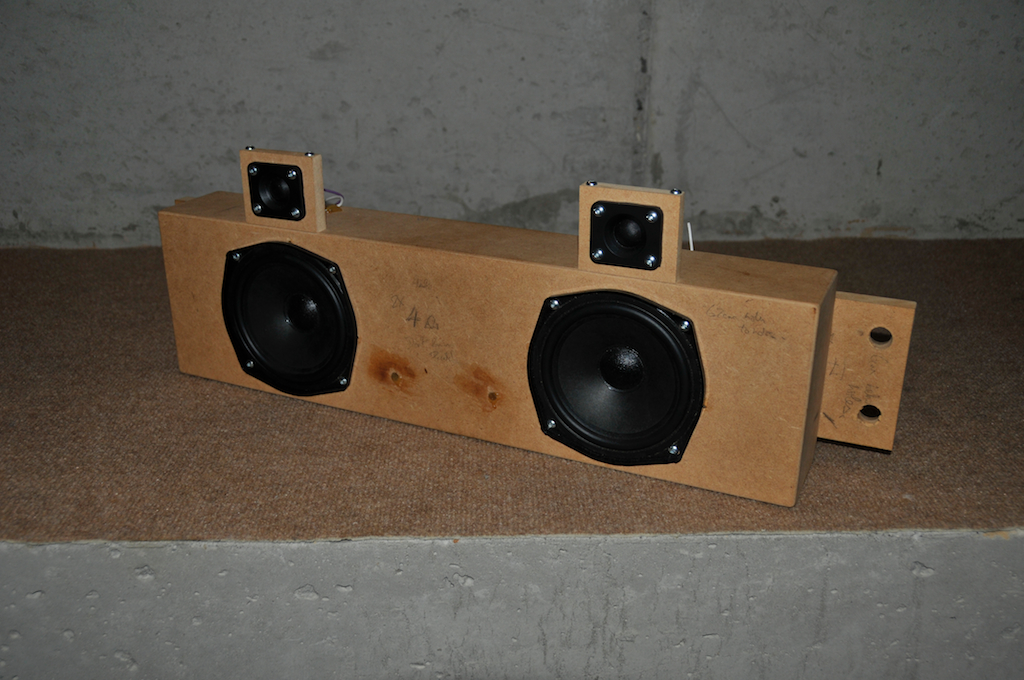
Note that, at this point, we are only considering the acoustic capabilities of the prototype. So, we won’t spend a lot of time tuning it, since there won’t be a lot of listening done to it. A rough tuning is done to clean up the serious problems, but the question being asked at this point is something like “do we have the hardware that can deliver a sound performance that we can work with?” If we were building a car, this would be like having the engine on a test block, checking to see if we are going to get the necessary horsepower out of it – we wouldn’t be taking it out for a drive yet.
So, we do a rough tuning of the prototype, have a quick listen, do some measurements and see if we’re in the ballpark – do we have a “go” or a “no go”? If it’s a “go” then we move on.
One of the big problems with Prototype #1 is that it doesn’t have the same shape as the final product. So, although we can use filtering to make this loudspeaker have the magnitude response we want in one direction – typically on-axis (which is usually, but not always, directly in front of the loudspeaker), it will not have the same off-axis or power response of the final product. This is because the off-axis and power responses of a loudspeaker are primarily determined by the physical shape of the loudspeaker itself. (For a slightly more detailed discussion of this, read this.) If the final loudspeaker is going to have a circular face, and the prototype is a rectangle, then we have no idea how the final product will behave. This is one of the big reasons why we don’t bother tuning Prototype #1 very carefully, since the off-axis and power responses are significant components in the overall “sound” of a loudspeaker. So, we have to build Prototype #2 which is shaped a little more like the final product.
Prototype #2
The second prototype, shown below, looks more like the final product – particularly in the shape of the “baffle” – an acoustical word meaning “the face of the loudspeaker where the drivers are mounted”. You can see that this prototype now has circular faces with a sharp angle between the front and the side/back of the enclosure. This shape has a very different acoustic effect (to be more precise, “diffraction” – but that’s a topic for a future posting) than the smoothed right angle in the MDF box in Prototype #1. So, with this prototype, we can get a much better idea of the off-axis and power responses of the final product. If we see something really problematic at this point, we enter into negotiations with the designer, since it means we are going to ask him or her to change the shape of the loudspeaker.
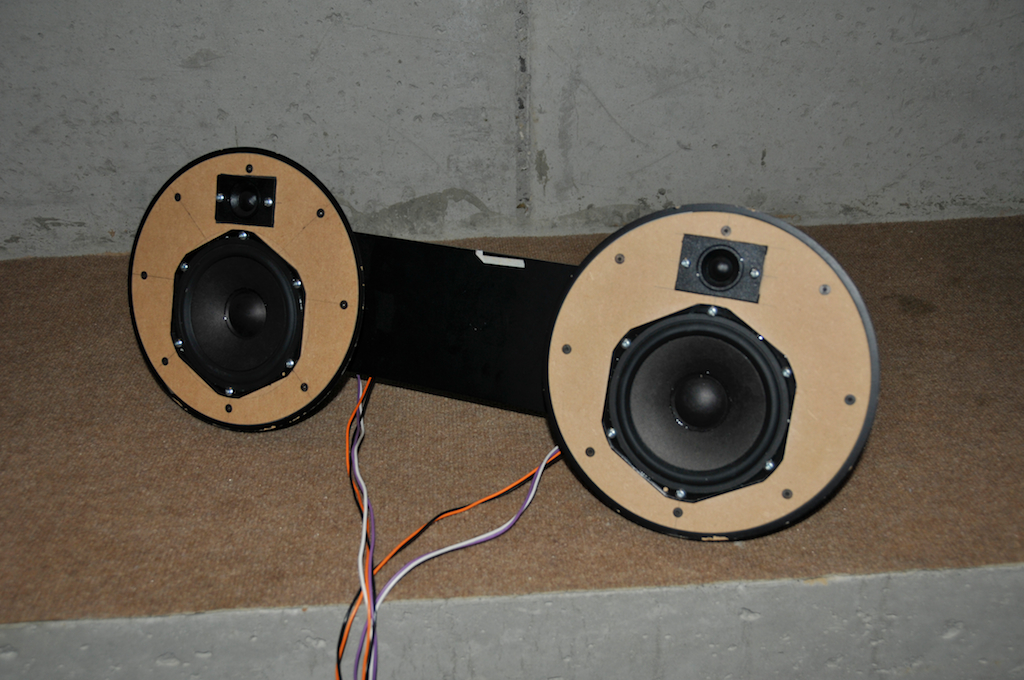
You’ll also notice in this photograph that the tweeter and the woofer have changed since Prototype #1. This may be either because we found out that there is another off-the-shelf driver available that better suits the requirements of the product – or it’s because we have gone to the manufacturer of the driver to get changes made to the device to make it better suited to the application. (This wouldn’t be surprising, since most drivers are not designed to be put in enclosures as small as the ones we use. In fact, most of our loudspeakers have loudspeaker drivers that have been customised for us specifically for the requirements of the finished products.)
Looking at the back side of the prototype in the photo below, you can see 8 wires coming out. There are two wires connected to each driver, and there are four drivers – two woofers and two tweeters. When we’re measuring or listening to the loudspeaker, these are connected to external amplifiers. Early in the process, we’ll use large, rack-mounted professional amplifiers, but as we get further through the development we’ll start using amplifiers that are more like the the final hardware.
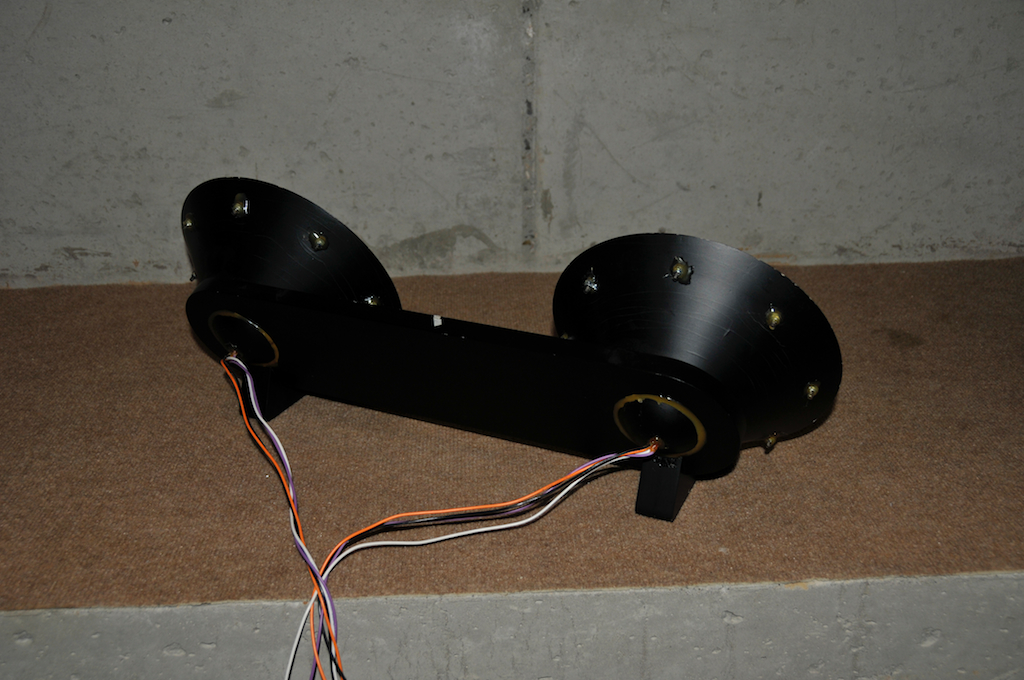
Prototype #3
So far so good. This time, the changes are more evolutionary than revolutionary. We get some more changes made to the drivers, and we make a model that is even more similar to the final shape of the product. If you look carefully at the difference between the second and third prototypes, you can see that the drivers have moved slightly. In Prototype #2, they were directly centred in the circular front, however, in Prototype #3, they’ve shifted slightly. Depending on the product, this might be due to acoustical reasons, but it could also be due to other reasons, such as the necessity to make space for components (like printed circuit boards) inside the enclosure.
As you can see in the photo, Prototype #3 doesn’t have any MDF parts – actually this one was milled out of a block of plastic. However, these days, we don’t do that any more, we use 3D printers. Unfortunately, we can’t start to do a detailed tuning of the loudspeaker yet, since the plastic that we used to use in the old days for milling and the plastic that comes out of a 3D printer is different from the plastic that gets used in the final product. As a result, the vibrations from the cabinet (for example) will be different in this prototype than in the final version. And, since a part of the final tuning is compensating for vibrations in the loudspeaker cabinet, there’s no point in tuning yet.
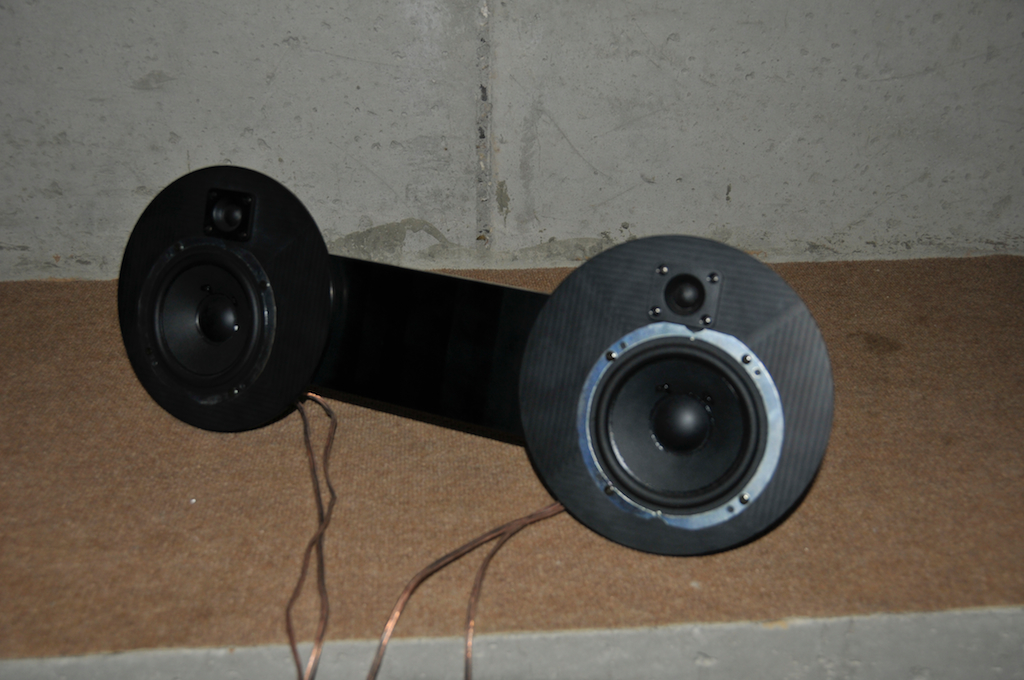
A funny side-story here. During the actual development of the BeoSound 8, we were doing a test on a prototype that looked exactly like this one (well, not exactly, it was grey…) in the Cube. It was sitting on a small platform on the crane (which hangs from the ceiling), about 6 m off the floor. The test was called a “bass capability” measurement where we put low-frequency tones into the loudspeaker at increasing levels until we reach a pre-determined amount of distortion. Then the frequency is changed and the test is repeated. Well, the test was running, and from the control room, you could hear a “boooooop … boooooop … boooooop … boooo ……… crash” Well, it turned out that the loud low frequency tones caused the prototype to slowly hop along the platform until it went over the edge and crashed on the floor. There wasn’t much left of it, so we had the black one made.
Again, as you can see in the photo below, we’re still using external amplifiers to drive the loudspeaker for measurements and listening.

In the next two photos below, you can see the prototype on the crane in the cube. You’ll notice, particularly in the first photo, that it’s securely clamped to a block of aluminium, which is also clamped to the crane itself. We wouldn’t want it to fall off and crash to the floor, now, would we?
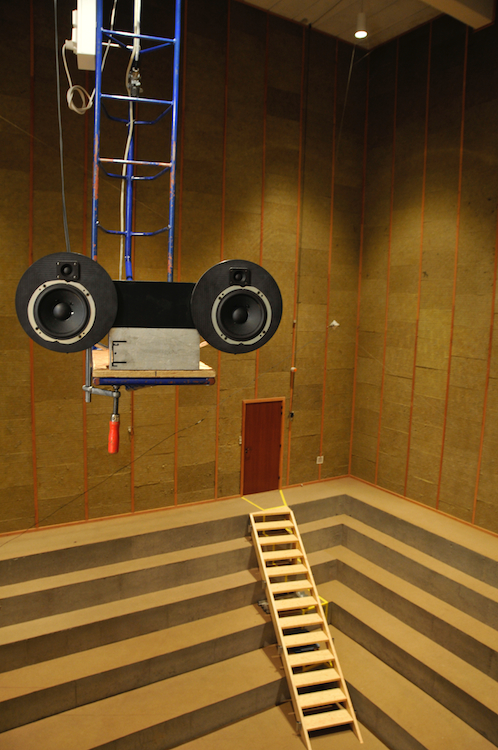
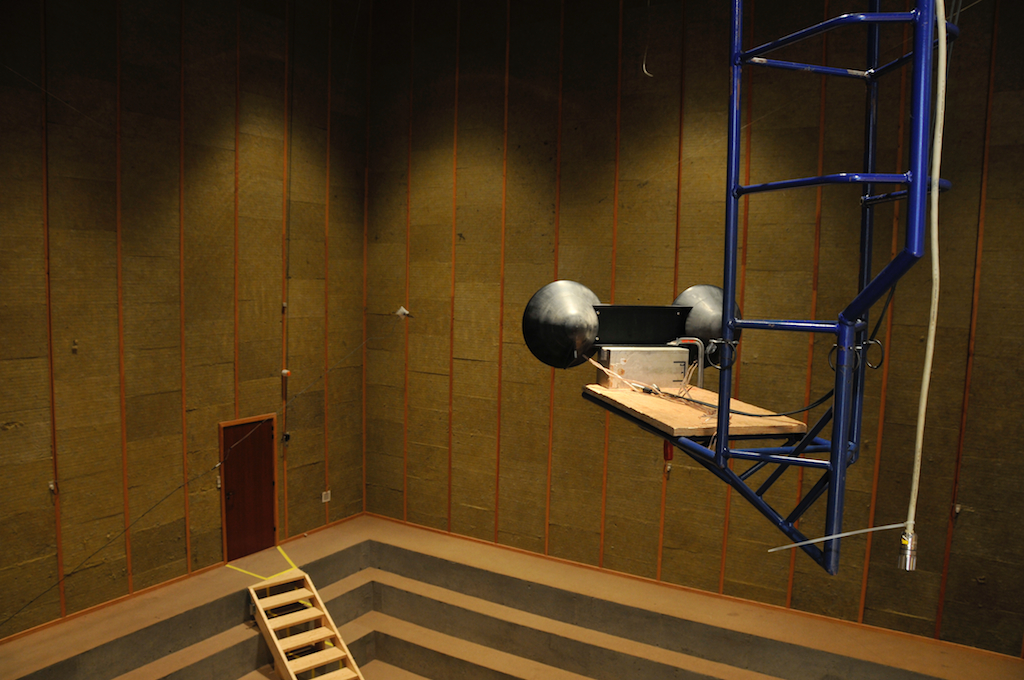
Prototype #4
At this point, we’re getting really close to the end. The production line is being set up, with the machinery being made to build the components in the product. So, we start looking at the early models that are coming off the production line. This means that we’re testing a product that is very close to being the final product, but it also means that we’re “de-bugging” the production line itself. This is why the prototype shown in the photo below looks like the final product – but it really isn’t.
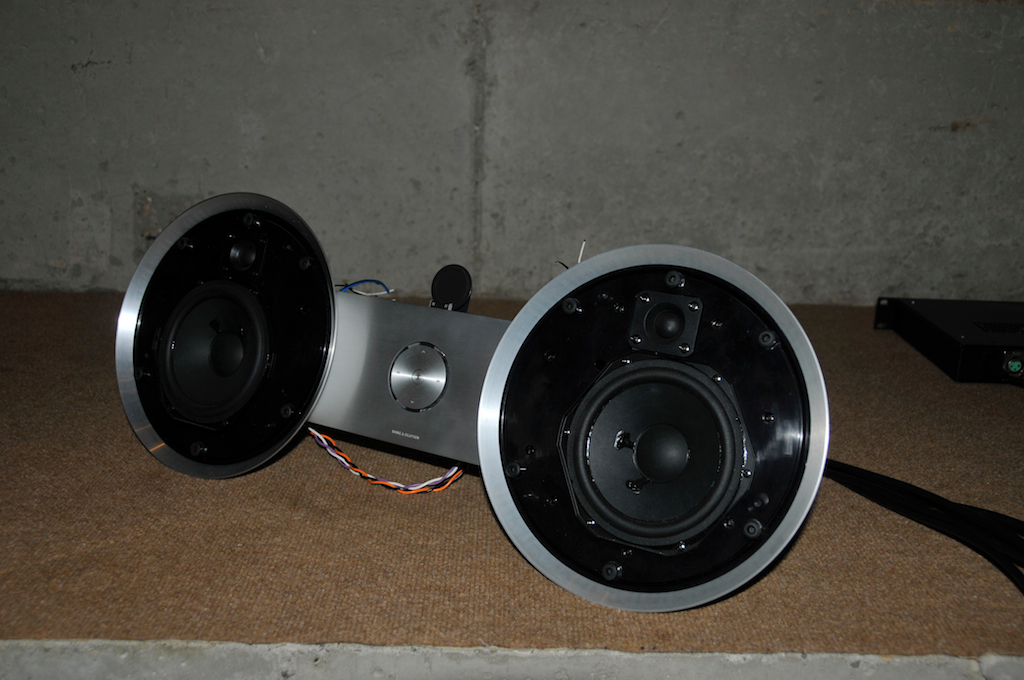
If you take a look at the photo below, you can see that we still have lots of wires having out of the back of the loudspeaker. Some of these are connected to the loudspeaker drivers themselves, because we’re still driving them with external amplifiers. However, there are a lot more wires there. The extra wires are connected to thermal sensors. We’ll come back to those later.
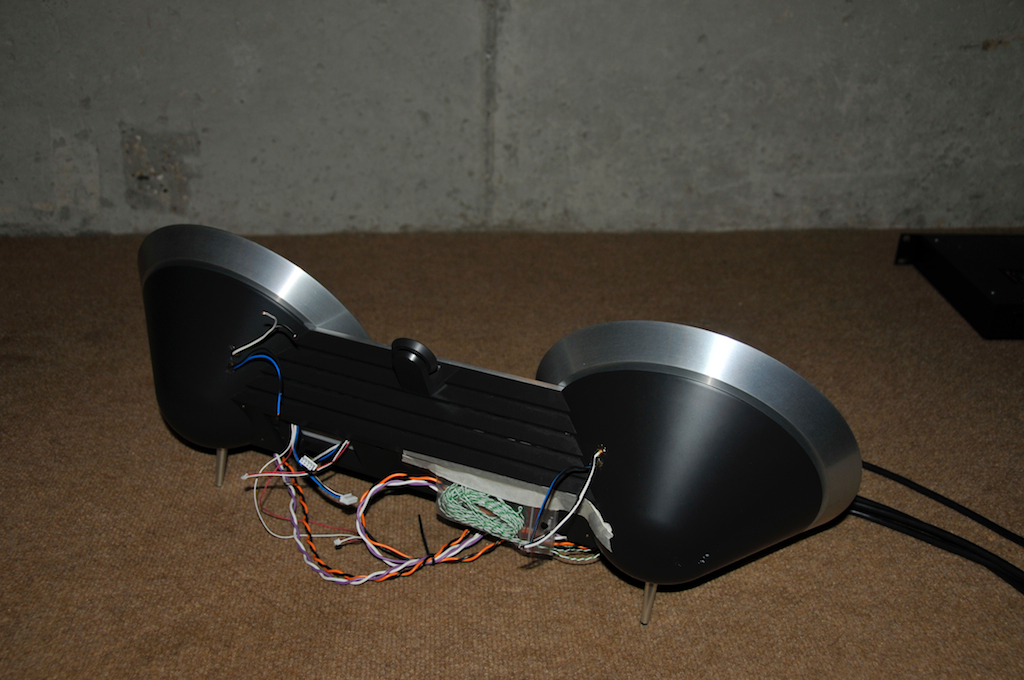
Since this prototype is basically acoustically identical to the final product, we can start working on the sound design of the loudspeaker. This is a three-step process, consisting of listening, measuring, and listening.
Step 1 is to ensure that the loudspeaker doesn’t suffer from any problems with something called rub & buzz. When a woofer moves in and out of a loudspeaker cabinet, there is a considerable amount of vibration sent through the system, either because the woofer is mechanically connected to the rest of the system or because of the large changes in pressure inside the loudspeaker enclosure. If there are any leaks in the cabinet or if two parts can rub together inside, then these vibrations will cause buzzing (which can sound a lot like distortion) at very specific frequencies. These are usually so bad that, if they aren’t fixed, we can’t measure the acoustical response of the loudspeaker. So, these problems get fixed by hand by using stuff like glue, felt, or foam weather stripping. There are two good things about this: the first is that we get a well-performing prototype that we can work with. The second is that we learn what needs to be fixed on the production line to avoid these problems in the final products.
Step 2 is to measure the loudspeaker in the Cube (a 12m x 12m x 13m room) to see how it behaves both in the frequency domain (i.e. what does its magnitude response look like) and the time domain (i.e. when you send in an impulse, are any frequencies ringing longer than others). The acoustical engineer and the DSP engineer work together at this point to look at the measurements and firstly determine whether any physical changes are needed in the loudspeaker to correct problems in its acoustical response. Once these problems are corrected, the difference between the desired response of the loudspeaker and the actual response of the loudspeaker is analysed. That analysis is used to build a filter that reduces the difference so that the we get the desired response from the loudspeaker – at least according to the measurements. For example, if the loudspeaker has too little bass and a bump in its response at 2 kHz, then we will boost the bass and put in a dip at 2 kHz. I’ll go into a lot more detail about this in a future posting.
Step 3 is to listen. The loudspeaker with its corrective filter is brought into the listening room and we start playing music through it. We don’t start fiddling with equalisation right away. The first thing to do is to listen for problems that don’t show up in the measurements. If we detect any problems in the listening room, then we go back to the measurements to see if we can find out why something sounds weird. This puts us in a loop of listen – find problem – fix problem – listen some more – etc. until we run out of problems with physical solutions. Finally, we start listening to music and equalising to get the loudspeaker to sound as we want it (whatever that means). So, we go into the listening room and do this (this usually takes between 3 and 5 days if all goes well). Then we go to a different room (like, say, my living room at home, for example) and start tuning from scratch again. This process of tuning in a room is done in 4 or 5 rooms, resulting in one tuning filter for each room (usually I wind up with between 20 and 40 equalisers for a typical loudspeaker in each room). The problem here is that some of the filters that get put in to clean up the sound of a loudspeaker in a room are actually to correct problems in the room – not the loudspeaker. This is why we do the tuning in more than one room – the different tunings are taken and only the corrections that are common to more than one room are implemented. (For example, we have a room mode at 55 Hz in the main listening room at B&O – so I’ll put in a filter at 55 Hz to reduce that problem when I’m tuning in that room. However, since your living room does not necessarily have a mode at 55 Hz, then that correction should not be part of the loudspeaker.)
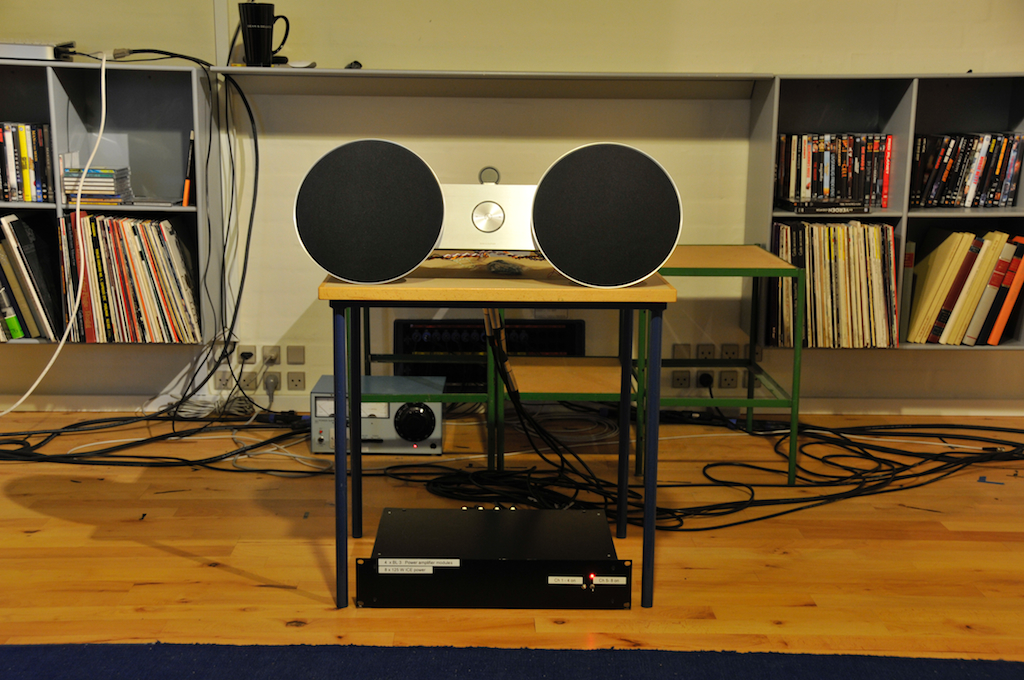
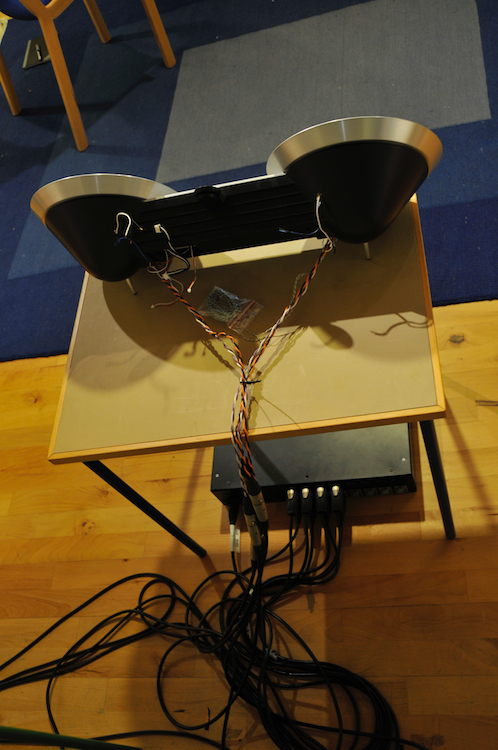
After the sound design has been finalised, then there are three more things left to do.
Firstly, the filters for the position switch (free / wall / corner) need to be tuned (using measurements from the Cube) and verified (by listening to music in different positions in different rooms).
Secondly, the final thermal tests have to be performed. For this, we connect the outputs of the thermal sensors (seen in one of those photos above) to a computer and we start playing some techno music really loudly, and we go home for the weekend. When we get back, we have a log file on a computer that tells us how hot the various components got and how that related to the music that we were playing. This tells us how close the loudspeaker components will get to their thermal limits in real life. Using this data, we can program the DSP to not allow the loudspeaker that you purchase to get hotter than it should. This was explained (sort of) in a previous posting.
Finally, we program a bunch of early production models with the “final” software and send them home with various people in the company for “real world” testing.
Production models
Once the production starts for real, we get the first samples that come off the line so that we can measure and test them to ensure that their performance and sound matches the prototypes that we worked on. Sometimes this doesn’t just mean putting the production model in the cube – sometimes it means something a little more customised. For example, for the BeoSound 8, we had to build a custom test rig and software to ensure that the fabric on the grilles was properly attached to the plastic backing. You can see the prototype of this test setup in the photo below.
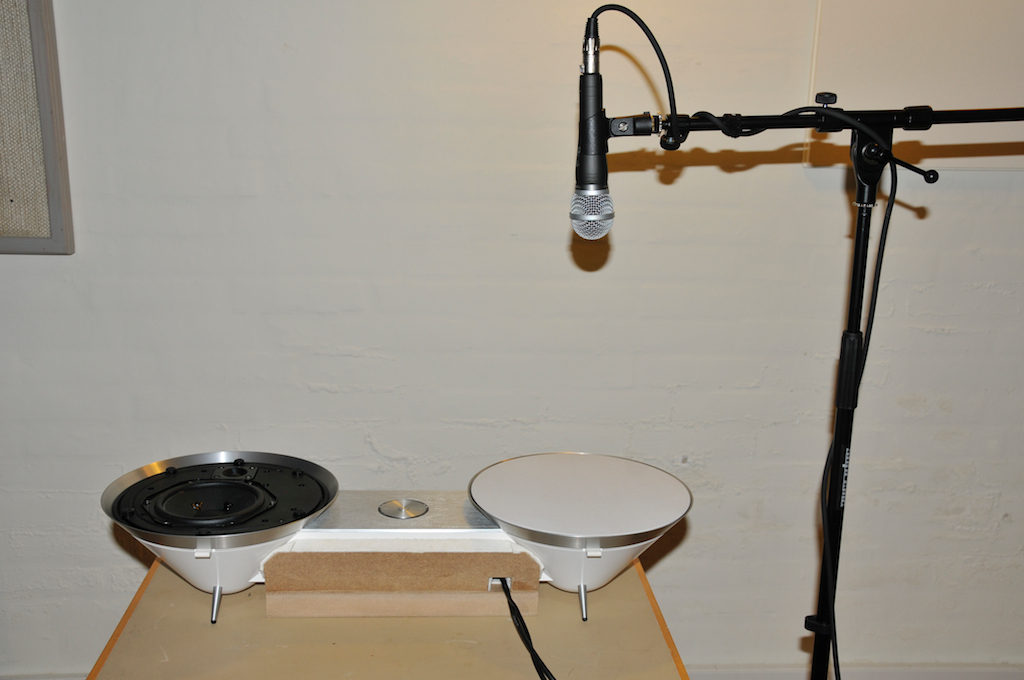
Finally, we’re done! We sign off the production models and give the go-ahead to start shipping to the dealers.
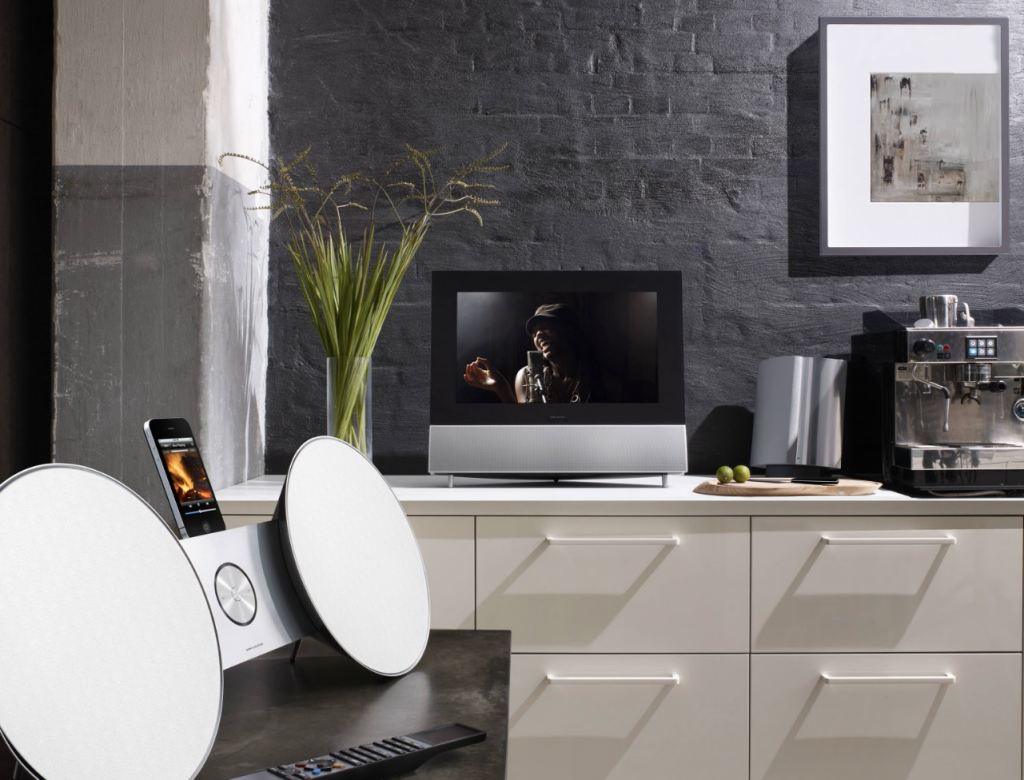
Of course, the story I’ve told above is sort of skipping over a lot of details – but I’ll fill in some of those holes (at least partially) in future postings.
Gabriel says:
I’m somewhat of a recent B&O convert.
I got the BeoPlay A8 when it arrived and liked it so much I purchased its little brother Beolit 12 to use outdoors in the summer. A year later, here I am with a pair of Beolab 9s in my living room and a Beovision 11-55 mk2 on its way to be delivered next week.
It’s the quality and craftsmanship that goes into these products that have made me a B&O fan, and so I really appreciate these posts. I can only hope you will continue to detail the development processes behind the products I love.
Great work.
Jeff says:
I found it interesting that you’ve gone to 3D printing over machining prototype cabinets out of blocks of material. As that was most likely done with computer controlled CNC machines, it’s especially interesting. Replacement of one tech with another, I think the market for 3D printing is going to change a great many things in the product development cycle.
SadBeosound Owner says:
I recently acquired a Beosound 8. A lot of “rub & buzz” emanates from the central column. Clearly there is a significant need for additional mechanical separation/isolation from the woofers which cause the buzz (spehich sounds like bad chuffing noise and bass distortion).
geoff says:
Hi,
How old is your BeoSound 8? Was it previously owned, or did you buy it new?
Cheers
-geoff
Patrick says:
Thanks for sharing your work! Would have never thought there were so many prototypes.
B&O is one of my favorite Danish companies being part Danish myself. Would love to work with more Danish connections!
Gai says:
Thank you for sharing this!
Amazing process you having there, it’s sounds like you have no limits of what you can achieve per product
I imagine how fun it is and super fruitful to measure vs listen by different ears and opinions of each and every person in the listening room has.